前言
现场管理只有三个基本要素:人、物、地;现场变更,只有物流和信息流;作为现场经理、生产总监、车间总监、团队领导,必须仔细分析和研究三个要素和两个过程,发现问题、原因和答案。
简单来说:车间管理10大法则:
检查工艺流程;
调整平面图;
计算生产线上的计算;
减少动作;
搬运时空压一压;
提到人机效率;
关键路线缩一缩;
现场环境变化;
视觉管理;
找根本问题。
本文旨在为现场管理者提供分析和创造现场管理的思路和工具。如果你掌握了它,你可以在不花一分钱的情况下从科学管理中获得效率和效益。
一、检查工艺流程
描述过程步骤和传输路线的图表称为过程图。它包括缝纫和其他工作流程,但本质是一样的。它可以用图像表来表示复杂的过程。
工艺流程或工作流程是单位工艺或工作的总路线。它生动地反映了工艺或工作程序、部门和程序之间的连接、判断或检查后的处理程序。服装企业或部门发现问题时,应从流程入手,分析现有生产工作的全过程,哪些流程不合理,哪些倒流,哪些停顿,哪些流程路线和环节可以取消、合并和简化?分析判断流程图的各个环节是否处于控制状态?检查能起到检查作用吗?各部门的横向联系到位吗?是否畅通?是否需要建立或增加新的通道?通过流程图的各个环节和传输路线,分析各部门现有的工作功能是否到位,现有机构是否需要调整或重组?
俗话说,框架、菱形和线条是由组成的,但它们是使用它们的宝藏。让你的过程更加复杂,透视清晰,不想跑步!加一加,严格控制更可靠;通过,部门职能不会失败。减少,以换取大大提高效率,确定,有规律,不争吵!
二、平面图上调一调
一些工厂在工厂早期没有仔细设计现场布局和设备布局,或由于生产、设备、破坏布局,或由于产品结构的变化,导致工厂或设备布局不合理,使产品和工件运输路线过长,这是浪费隐患,必须决心改变。
工艺流程图上看不到平面路线,流程图上的箭头可能要走几十米,所以要在平面布置图上进一步寻找好处。
通过分析操作模式和设备配置,找出不合理的部分,合理调整新的设计布局,缩短工艺路线与操作人员的行走距离,减少不必要的资源浪费。
有时,设备的移动可以节省几十米甚至几百米的距离。有时会节省更多的空间。
三、计算流水线上的计算
生产线和装配线应以相同的节奏平衡生产。有些企业经常有早期工作、后期工作、早期工作和情况。一个原因是移动模式不合理,另一个原因是节拍不平衡。
由许多不同长度的木板组成的桶不是最长的木板,而是最短的木板。同样,在装配线上,最慢的人是决定装配线最终效率的人。生产线或装配线的平衡效率=每个工序净运行时间总和/最长工序运行时间×人数。许多生产线的平衡率通常不到50%。如果简化长期流程、加速、更换或拆分,则通过合并和增加短期流程来平衡流水线。整个生产线的生产效率将大大提高,个别流程缓慢造成的窝工和积累将被消除。
四、减少动作要素
任何操作都以人工行动为基本单位,厂等劳动密集型企业。行动是产生效益的一个非常重要的因素。
动作分析的主要目的是消除多余的动作、无效的动作或缓慢的动作,如弯曲作业、蹲作业、作业场所不光滑、没有合适的工具、寻找人和事物等,以最省力的方式达到最大的工作效率。
这项研究几乎不花一分钱就能大大提高生产效率。例如,在现实生活中,为什么有些人做饺子比普通人快得多?为什么有些人比普通人快得多?这是因为他们掌握了一些技能,并以最经济的行动完成了任务。
以饺子为例。很多人会用八个以上甚至几十个动作包饺子。如果你把勺子夹在右手的拇指上,不要放下。按照以下程序包饺子:左手拿皮——右手挖馅——双手合拢捏饺子——左手放饺子。包饺子只需要四个动作,效率是普通人的两倍!
五、搬运时空压一压
据统计,25%到40%的加工费是搬运费;70%到80%的过程时间是搬运和停止的时间;85%的工厂灾害发生在搬运过程中。因此,压缩处理非常重要。改进处理,优化处理数量、空间和时间。
一是减少搬运次数和次数;
二是尽量缩短搬运距离,减少搬运路线和次数;
三是缩短搬运时间,减少搬运时间;注意方法管理协调,尽量使用重力滑坡或输送带等非动力。
搬运合理化的原则是对搬运材料几乎没有损失;搬运方法应科学文明,消除野蛮和粗糙;安全、适当和冒险;尽量减少暂时放置的机会;合理规划工厂布局可有效缩短搬运距离。工厂规划定局时,也可以通过合理的规划过程有效缩短搬运距离。
六、提到人机效率
人与设备是矛盾的。如果处理不当,人们会等待机器或机器。人与设备构成了人机工程之间的关系。在分析过程中,应同时分析操作人员和机器的工作情况,是否有窝工、等待和无效时间。通过调整工作顺序,可以改善人机合作,寻求合理的方法,协调人机操作,尽量减少等待时间,充分发挥人机效率。为了人机联合运行的好处,挤出等待时间就像挤水一样。
七、关键路线缩一缩
几乎任何产品都由几个部件组成,通常分为几条线或几个工艺生产,以后应逐一组装。不同工艺的工作量在形成零件和零件的过程中是不可避免的。
这将相互限制未来的生产。工作量小的过程将有大量的空闲时间,而工作量大的过程将没有一刻的休息时间。换句话说,零时差已经成为生产的瓶颈。零时差的过程被称为限制服装厂或车间生产能力和交货期的关键路线。找到关键路线后,应从非关键路线中抽调人员和财产,加强关键路线,或以平行、交叉的形式缩短关键路线,不断修改和优化计划,实现缩短时间表、节约成本的最佳目标。
生产总监的基本技能是根据计划和生产能力计算和找出关键路线。二是不断压缩关键路线等路线,实现时间和成本的综合优化。有两种方法:
第一种方法是时间优化。它是在人力、设备、资金等保证条件下寻求最短的工作周期。它可以争取时间,快速发挥投资效果。利用时差,将部分人力物力集中在非关键路线的关键路线上,或分解操作,增加操作之间的平行交叉,增加人力设备投资,利用新技术缩短关键路线的延续时间;
第二种方法是时间-成本优化。项目成本可分为直接成本和间接成本。直接成本是指与织物或辅助材料等各种操作直接相关的成本。间接成本是指与各种活动无直接关系但随时间变化的成本。工程周期越短,间接成本越小。-成本优化是寻求直接成本和间接成本之和的最低时间。
八、场所环境变化
分析生产、工作环境是否满足生产、工作和生理需求,分析缺乏项目和媒体,提出不同类别的改进建议,开展整理、整改、清洁、清洁、质量、安全六项活动,始终保持A状态,不断改善B状态,随时清除C状态,让员工保持强烈的士气和良好的技能,所需的物品是可取的,不需要随时清除,现场环境光滑、整洁、美化、安全、文明,使现场和环境实现时间和空间的整体优化。
看视觉管理
人脑的视觉信息高达80%。因此,视觉交流和指挥更直接。利用直观、色彩合适的视觉感知信息组织现场生产,以图表、图片、照片、文字注释、标志、符号为视觉管理工具。解释、认知、警告、判断、行动等功能易于实现。因此,视觉管理也可以称为可见管理和可视化管理。
找出问题的根源
每天寻找差距,第二天做得更好——这是海尔模式原创性中非常重要的一点,不断寻找问题,分析问题,不断改进现场,这是质量改进,8D工作法、CIP等待活动的共性。这促进了管理和运输过程,使企业处于良性循环。
如果你真的使用现场改进的车间管理10大法则,你会发现这些武器是非凡和不可战胜的。您会惊讶地看到:工艺路线畅通,平面布局合理,装配线上窝工消失,节奏更均匀,操作效率高,操作方便,生产平衡,人机紧密结合,管理简单,精益生产形势更快、更好、更短、更光滑、更酷!
加客服微信:FX951741939,开通VIP下载权限!
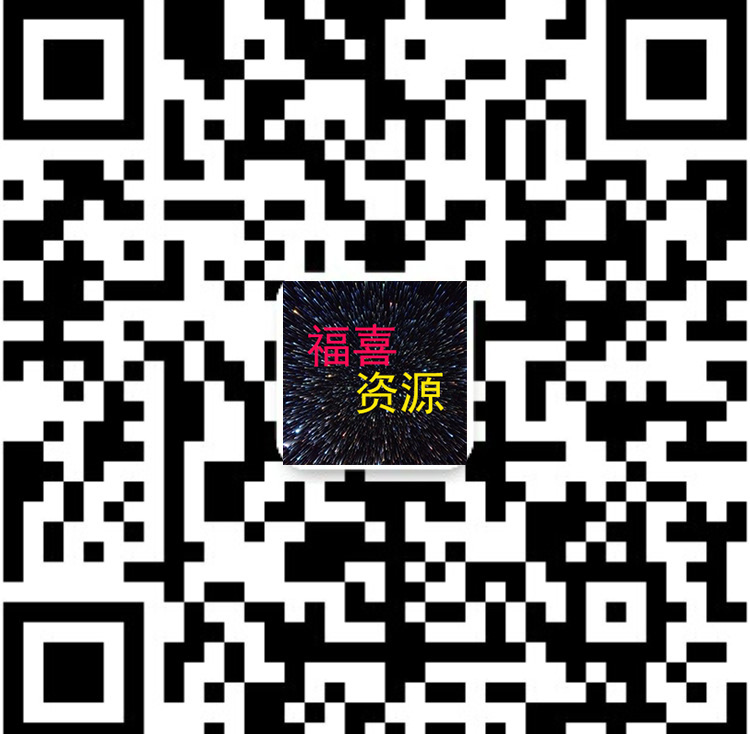